Airbus and Boeing Prepare for Increased Output of Jets with Thermoplastics
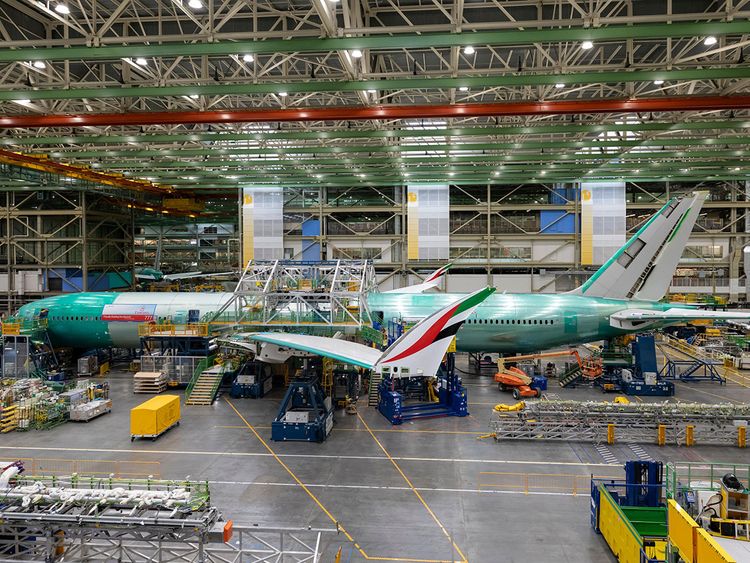
Airbus and Boeing are preparing for significant increases in the output of their next-generation workhorse jets, with plans to reach production levels of up to 100 units per month each, according to industry sources. This ambitious plan involves exploring lighter plastic materials and robotic assembly techniques.
Amid weak supply chains and potential delays in future engine developments, the world’s two largest aircraft manufacturers are still years away from launching projects to replace their aging Boeing 737 and Airbus A320 series, which continue to see strong demand.
However, both companies shared their progress on researching materials and manufacturing techniques for future models at a technical conference at a Paris composites fair this month. They discussed how to improve the speed and efficiency of production for the next generation of aircraft.
“The goal is to recommend the best approach to transition to the next airplane program,” said Randy Wilkerson, who represents Boeing in a NASA research project for high-capacity manufacturing, called HiCAM, during his presentation at the JEC World conference in Paris.
The current models that future jets will replace are primarily made of aluminum, using methods that have been perfected over decades. But composites are now being explored due to their lighter weight and aerodynamic design.
Composites, which are already widely used in larger jets such as the Boeing 787 and Airbus A350, provide fuel and emission savings, though they currently require time-consuming handling in pressurized autoclave ovens.
To meet the demand for much larger numbers of smaller jets, both companies are increasingly studying the use of novel materials like thermoplastics, which can enable faster production speeds.
Industry experts noted that ongoing studies expect future production to reach 80 jets per month for both Airbus and Boeing—more than double Boeing’s current production rate, which has been affected by past safety issues, and higher than Airbus’ delayed target of 75 per month.
However, sources told Reuters that both manufacturers are pushing the limits of production capacity and aiming for up to 100 jets per month each—an impressive pace equivalent to producing one 200-seat jet every few hours.
Both Boeing and Airbus declined to comment on these plans.
Thermoplastics: A Game Changer?
The use of thermoplastics in aerospace manufacturing is generating significant interest. The industry has been using composites since the 1970s, but these materials were never produced at the scale now being considered.
Analysts believe that production capacity will become as important as design in the future jet industry, especially as the West faces increasing competition from China.
Until now, structural parts for jets, like those used in the Boeing 787, have been made with thermoset composites, which retain their shape and strength once cured in autoclaves. However, future techniques could involve faster curing methods, providing a lower-risk approach with significant potential, according to Wilkerson.
Another promising technique being explored is resin infusion, traditionally used in boat manufacturing. This could allow for automated production of certain components without the need for autoclaves.
The buzz around thermoplastics is growing, with Airbus, GKN, and others showcasing the world’s largest thermoplastic fuselage structure at the JEC World composites event.
One of the key advantages of thermoplastic materials is that they can be reheated and reshaped into a continuous, flowing aerodynamic form. “You can melt it and reshape it in any way you like,” said Lukas Raps from the German Aerospace Centre (DLR).
Such parts can also be welded using advanced methods, such as ultrasound, instead of being fastened with rivets, which would help reduce weight and increase efficiency.
Additionally, thermoplastics are less likely to require autoclaves, which represents a major time and energy savings when considering large-scale production increases.
“There is no doubt that thermoplastic materials offer opportunities that we don’t have with thermoset composites,” said York Roth, a leading researcher at Airbus in Germany, at the conference.
Any shift to welding rather than using traditional fasteners like titanium bolts could present certification challenges. Industry sources suggest that the next generation of aircraft will likely incorporate a mixture of approaches, rather than relying on a single technology.
The Future of Aerospace Composites
Though aerospace is a relatively small sector for composites, it plays a critical role in terms of value and research. Officials emphasized that there is no immediate plan to launch a new aircraft, as such a move could disrupt investor confidence, particularly following the recent supply chain crises and turmoil at Boeing.
“This demonstrator was never meant to fly, but it has been established to maximize learning,” Roth explained to the delegates.
Related news: https://suspicious-zhukovsky.67-21-117-18.plesk.page/category/air-travel-business/aircraft-finance/
Sources: AirGuide Business airguide.info, bing.com, yahoo.com