Engine Overhaul Surge: Challenges and Opportunities for Airlines
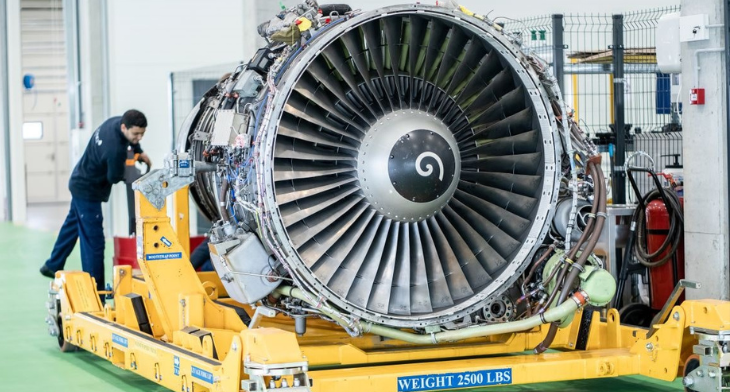
The aircraft engine repair and overhaul sector is experiencing unprecedented demand due to parts shortages, delayed deliveries from Boeing and Airbus, and an ongoing engine recall. This surge in activity has elevated the industry’s value from $31 billion pre-pandemic to a staggering $58 billion in 2024, according to Alton Aviation Consultancy.
With travelers flocking to the skies in record numbers this summer, airlines are grappling with extended wait times for engine repairs and overhauls. The aviation industry’s recovery from the pandemic has been marred by significant challenges, including workforce shortages and supply chain disruptions.
American Airlines Expands In-House Engine Overhaul Capabilities
To address these challenges, American Airlines is significantly ramping up its in-house engine overhaul operations. The airline is set to boost its engine overhauls by approximately 60% from 2023, targeting more than 16 engines per month by year-end, compared to just five per month in 2022. This increase is being facilitated at American’s extensive 3.3 million-square-foot maintenance facility at Tulsa International Airport, the largest of its kind globally.
The focus at the Tulsa facility is on overhauling CFM56 engines, produced by a joint venture between GE and France’s Safran. These engines power American’s older Boeing 737 and Airbus A320 aircraft, which make up the bulk of the airline’s fleet of over 960 aircraft. American’s Chief Operating Officer, David Seymour, noted that in-house overhauls are completed in less than 60 days, compared to 120 to 150 days or more at external shops.
Industry-Wide Bottlenecks and Delays
The bottleneck in engine repairs largely stems from the industry’s struggle to rebound from the pandemic. Many companies reduced their workforce during the travel downturn, leading to a shortage of skilled technicians when demand surged. This shortage, coupled with delays in receiving essential components and aircraft seats, has exacerbated the problem.
Airbus and Boeing have also faced challenges. Airbus recently cut its aircraft delivery forecast due to supply chain issues and delays in receiving landing gear and engines. Meanwhile, Boeing has been managing delays and safety issues following a midair incident involving one of its 737 Max planes.
Rising Costs and Supply Chain Issues
Engine overhauls, which typically occur every 7,000 flights, are not only time-consuming but also expensive, costing up to $5 million per engine, and potentially double for wide-body aircraft. The cost and difficulty of finding flawless parts, such as compressor blades priced at $30,000 each, contribute to the backlog.
Additionally, a recent recall of Pratt & Whitney engines has further strained the supply chain. This recall, coupled with deferrals of new jet deliveries by low-cost carriers like JetBlue Airways and Spirit Airlines, has compounded the issues facing engine shops.
Lucrative Market for Engine Makers
Despite these challenges, the high demand for engine overhauls has proven lucrative for engine manufacturers. GE Aerospace reported $11.7 billion in revenue from engine maintenance, repairs, and overhauls in the first half of 2024, representing 65% of its total revenue. The aftermarket segment of the engine business, akin to the “razor-razor blade” model, continues to be a significant profit driver for engine suppliers.
The ongoing challenges in the aircraft engine repair industry highlight a complex interplay of supply chain issues, rising demand, and strategic adjustments by airlines. As the industry navigates these hurdles, the focus remains on balancing efficient operations with the growing need for reliable and timely engine maintenance.
Related news: https://suspicious-zhukovsky.67-21-117-18.plesk.page/category/air-travel-business/aircraft-finance/aircraft-supplier/
Sources: AirGuide Business airguide.info, bing.com, cnbc.com